Higher plant and employee productivity through digitization
AXAVIA's SAM software is a maintenance software for managing your plants and machines. So that you always have an overview of all plants and machines in your company that require inspection. Professional maintenance and servicing not only extends the life cycle of a plant, but also guarantees you minimum downtimes with optimal resource planning.
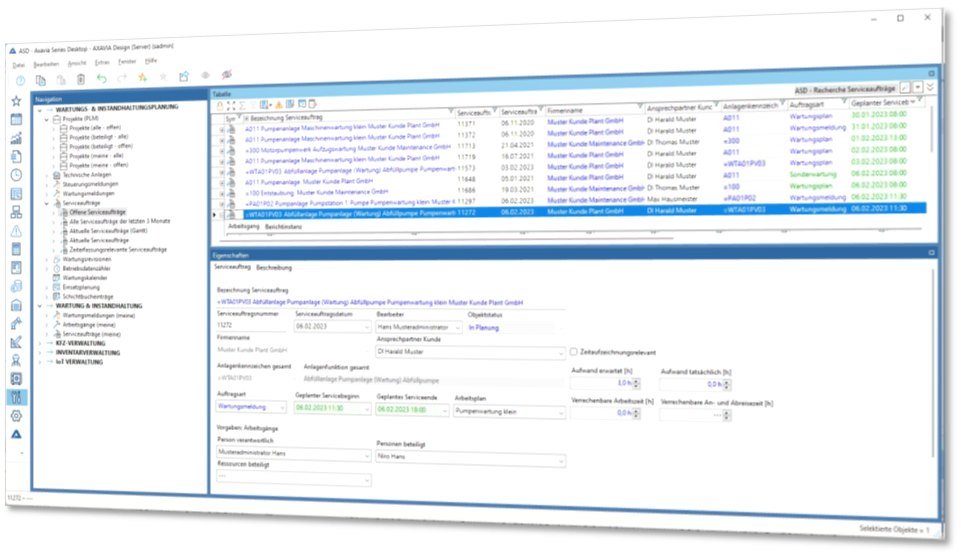
All open service orders
Detailed information about the service order
Plant documentation made easy
Organize your sites and plants in projects and define your plant structures there. Store your documentation for your plants in the integrated document management and have access to your current documentation at any time.
Plant structure and technical component information
The basis for the plant documentation is the mapping of the entire plant. For this purpose, a plant structure and optionally a location structure are used. This is also used at the same time to set up the labeling system. For the plant documentation, the corresponding components (tank, pump, motor, valve, mechanical assembly,...) are recorded with the technical data.
- Process data (operating temperature, operating pressure,...)
- Specification data (nominal size, motor power,...)
- Product data (item number, manufacturer,...)
- Operating data (serial number, operating hours,...)
Automated work & service plan
You define your service plans for the precise planning of service assignments. On the one hand, you define in a work plan which activities are to be carried out, which spare parts you need and which checks are to be carried out. On the other hand, you define how often the service call must be carried out using a series date definition.
- Service tasks
- Spare parts
- Checklists
- Series dates
Service orders at a glance
Create your service orders based on the maintenance plans for your technical systems and schedule them for your employees. The service order defines the work required to maintain the plant. It is used on the one hand for regular maintenance work and on the other hand also for malfunction operations from maintenance notifications.
The following information is managed:
- Equipment that should be maintained and what work needs to be done
- Time, duration and processor
This gives you an overview of the workload of your employees and additional resources. In a service calendar and a planning board, you always have an overview of when which service orders are to be completed by which employees.
Smart task & resource planning
Plan your tasks, work packages and milestones and have an overview of your deadlines.
- Expenditure expected
- Start, duration and end
- Dependencies Tasks
Tasks are assigned to resources, which makes it easier to manage unforeseen bottlenecks.
can be better managed. In addition to employees, equipment, rooms or components are also available as resources.
Deployment planning
On the one hand, the allocation of the employees to the maintenance orders or the corresponding tasks results in the resource utilization. On the other hand, this also results in the task list for each employee. The task list can now be displayed in the form of a Gantt chart for each employee, thus providing a clear overview of employee scheduling.
Optimized maintenance messages
Record and document the malfunctions of your systems and analyze where optimization potentials lie fallow.
Define priorities, error descriptions and priorities. Also store the corresponding solutions in order to immediately have a solution approach in case of recurring errors. The duration between error detection and error correction determines the duration for the correction of error messages.
Create the corresponding service orders from the maintenance messages to process the faults.
Working hours & travel expenses
For a service assignment, corresponding working hours and travel costs are also incurred. Document these in the service order and use this information on the one hand as time recording and on the other hand as a basis for billing the service order. The transfer to the billing takes place smoothly by setting the order to completed via a workflow after completion of the service order and passing it on for billing.
Service report with digital signature
From the service order, you generate a service report as a PDF document in which all relevant information (service tasks, checklist, required material, working hours, travel costs, test entries) is printed.
You can sign it digitally using predefined fields and the optional add-on product Signosign and send it directly to the customer right away.
Service orders on the web
For mobile processing, the service technician has access to a web portal with which he can process his service orders.
He has immediate access to his current service orders and can enter the data online.
He enters any checklists or test entries directly via the web portal.
- List of its service orders
- Service tasks with timelines
- Supplement spare parts
- Checklists with test entries
- Recording travel expenses and working hours
- Preparation of the service report
- Signature of the customer with Signosign
- Sending the service report to the customer
- Passing on the service order for settlement