PPS software for production planning -
all processes in production planned, controlled and monitored
Based on demand requirements and production orders, production planning is the core element in manufacturing. Plan, control and monitor all operations in manufacturing. Ensure that sufficient resources and materials are available for production. The module supports you in the entire process chain from the production order, to the delivery. In combination with time recording, you have control of the resources actually used at all times.
Sales products are broken down into individual items using the stored bills of materials and form the basis for requirements planning for the materials required. Predefined routings complement the planning and the necessary work steps and thus determine the resources to be scheduled. With the help of working time models and processing times AXAVIApps supports you in capacity planning.
The basis for order execution are the work sequences and target times defined by work planning in the routings. Other important data are the capacities of employees, machines and operating resources available in the current situation, i.e. the number of available working hours in the future periods.
Production planning made easy
You use the production plan to define the production steps that are necessary for the production of a product. If you need additional material for a production step, this is recorded via the material requirement. If products are created during a production step, a material yield is created. For the production steps, the required duration for the setup of a machine or the execution of a production step and the necessary resources are defined.
This means that all the necessary definitions have been made to automatically schedule a product in a production plan and to determine the corresponding work steps in production. Resource allocation can also be carried out largely automatically.
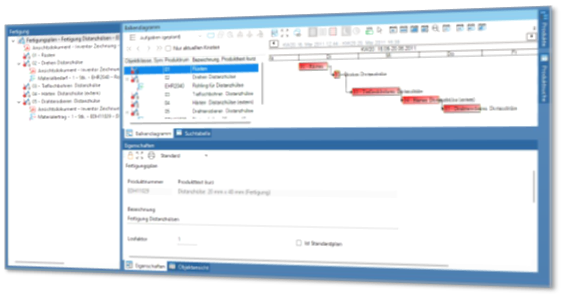
Production plan incl. view documents
Gantt - representation
Production order
Starting from the completion date, the individual production steps are scheduled using automatic backward scheduling, whereby manual readjustments can be made at any time. The stored resources and quantities are used to plan the duration. Release for production takes place via a corresponding workflow.
In a Gantt chart you have an overview of when you have to complete which tasks.
Material requirements determination & disposition
The basis for automatic requirements determination is the respective product structure from the material master. The product structure defines via the respective material requirements which additional materials (dependent requirements) are needed during production.
An MRP run determines on the one hand the material required and on the other hand the resulting yields. These can be planned stock withdrawals or requirement demands.
In addition to the required products, the corresponding dates are also automatically transferred and filled out in the requisition. The further requirements are then covered again by purchasing or renewed in-house production of the required components.
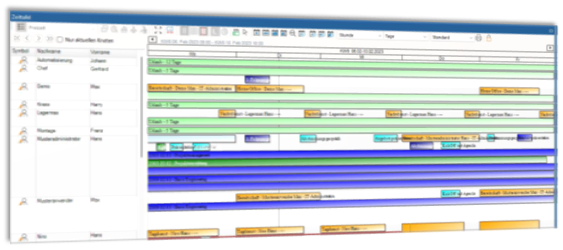
Resource utilization
On-time delivery through optimal resource planning
When is there still free capacity to give a delivery date for an order? These and similar questions are on your agenda. AXAVIApps provides you with the utilization of your resources at the push of a button. Free resources and overloads are instantly recognizable.
On the one hand, employees and machines, but also rooms or motor vehicles are available as resources for capacity planning. On the other hand, it is often helpful not to define resources in detail, but only to specify a resource group in the form of a department or a specific qualification in order to obtain the corresponding utilization information.
Based on the planned production orders with their production tasks with the defined resources (machines, workstations, employees), the resource utilization is determined.
Scheduling is done automatically with backward scheduling of production tasks based on dependencies and the defined completion date.
The balancing of resources in the event of overload is carried out manually by the work preparation department.
Work cards with barcode support
The respective production orders can be issued as work cards and thus form the basis for processing in production. The work cards serve as escort cards and
pass through production with the products. The work cards can be equipped with barcodes to enable efficient processing in production. On the one hand, the time bookings and, on the other hand, the status of the respective work steps are posted.
Use the work cards or run cards with barcodes either on the PDA terminal for feedback or with the warehouse app to conveniently perform warehouse movements.
Clear schedule & planning board
The basis for optimal scheduling is an overview of the pending production orders. When do which orders have to be completed? You also have access to the sales orders at any time and know when the delivery dates to the customer are due. If production orders are overdue and not completed, you will receive a corresponding notification. The result of the planning of the production orders, their production tasks and allocation to the resources is a concrete production plan for the production.
Different displays are available for the planned production orders:
Table
The tabular display is especially useful when you want to perform quick filtering, sorting or bulk editing of the data.
Planning board
The planning board shows you quickly and clearly which production orders are processed when on which machines and resources.
Gantt representation
The Gantt chart displays the upcoming production orders in a clearly arranged time and immediately shows you possible delays by displaying the status of the production orders in color.
Smart manufacturing feedback
For a quick and easy overview of the current situation in production, timely feedback of the completed work steps is especially necessary. On the one hand this is possible manually via AXAVIApps, on the other hand a barcode reader is an optimal supplement for the feedback. After completion of production orders a feedback to the PPS system takes place. For this purpose, the AXAVIA DBE terminal is available, which is optimized for feedback in production. This is preferably done via barcode support.
The feedback mainly considers 3 issues:
Time feedback
By scanning the start and end of the activity, the required working time is booked to the respective production task and provides the necessary information for post-calculation. In addition to the working time of the employees, this also includes that of the machines used. Thus, the machine time results in the corresponding costs, which are taken into account for further cost evaluation.
Quantity feedback
In addition to the working time, the produced quantities are of course of essential importance in order to control the further process. Any scrap quantities are also recorded at the same time.
Warehouse entrance
After completion of the production task and successful quality inspection, the corresponding quantities are also reported to the warehouse and are thus available for further use. Store the serial or batch number for the individual goods movements, which are always necessary in production, especially when assembling modules.